Digitally connected processes enable more flexible, (energy) efficient, individualized and cost-effective production. Management, administration and support processes should also not be neglected. This blog post will show you how process digitization can be successful.
There is more than just a hype behind the trend terms “Smart Production“, “Industry 4.0“, “(Process) Digitalization” and “Artificial Intelligence (AI)“. Rather, the terms express groundbreaking developments that cause fundamental changes in production and other business processes and influence the entire value chain.
According to Statista (2019), an estimated € 221 billion in sales in Germany in 2019 were already influenced by AI applications. The largest share of this is accounted for by the manufacturing industry, especially automobile production and, for example, mechanical engineering.
No matter what you want to call it, in the end it is always about the seamless connection of the digital and real world and the networking of the entire value chain. Digitally networked processes in Industry 4.0 enable a more flexible, (energy) efficient, individualized and cost-effective production. Management, administration and support processes should not be overlooked.
Companies are always looking for new and innovative solutions to meet the demands of a growing product variety and ever shorter product life cycles. This drives the networking of machines, people and services throughout the entire manufacturing process.
In addition to mere networking, Smart Production includes monitoring, data transport and its automatic analysis, virtualization and process planning.
More performance and process reliability - through digitalization
For instance, machines connected via the Internet are used in Smart Production to monitor and optimize the entire production process. The aim is to advance the automation of manufacturing processes and to improve production performance with the help of data analysis.
By analyzing the data stream of the machines of an entire factory – or even of several factories – the causes for the failure of machine parts, for example, can be checked more efficiently (Condition Monitoring). Smart Production also enables preventive maintenance, so that unplanned downtimes on equipment can be almost completely avoided (Predictive Maintenance).
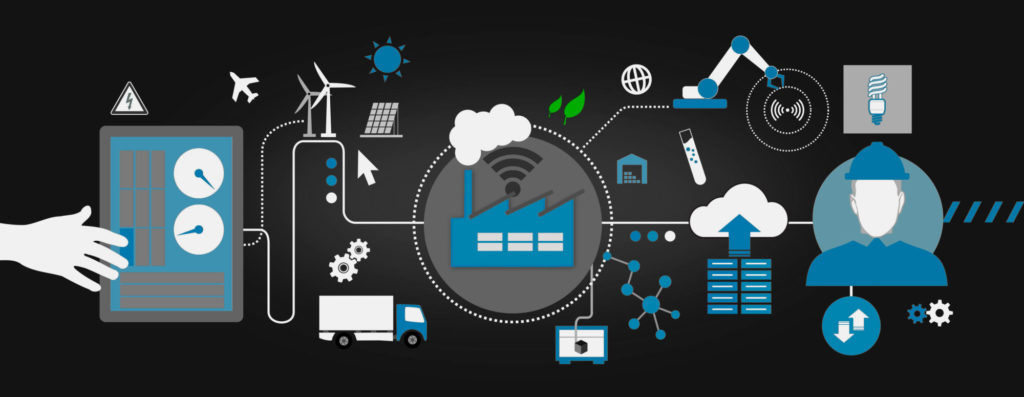
By analyzing the data stream of the machines of an entire factory – or even of several factories – the causes for the failure of machine parts, for example, can be checked more efficiently (Condition Monitoring). Smart Production also enables preventive maintenance, so that unplanned downtimes on equipment can be almost completely avoided (Predictive Maintenance). Trends in the data can be analyzed to identify process steps where production is slowed down or becomes inefficient due to the use of certain materials, for example.
The more widespread Smart Production becomes and the more machines are networked through the “Internet of Things“, the better they can also communicate (with each other) and support a higher level of automation. For example, Smart Production systems can automatically order raw materials when stocks run low or assign new production orders to less utilized machines as needed.
Standardized and digitized processes are also a means of meeting compliance and data protection requirements. The confidentiality of data and documents can be ensured by a more secure exchange of information. A high degree of automation prevents manual errors. In particular, however, digital processes enable a high degree of transparency and traceability.
The advantages of “Smart Production“, “Industry 4.0“, “Process Digitalization” and “AI” ultimately stand and fall with the available data basis (see also Intelligent control of business processes in times of digitalization) . With the networking of the value-added chain, there must be holistic data consistency and it must be possible to call up data in real time in order to be able to react quickly to current key figures – preferably (fully) automated.
How does process digitalization succeed?
In a recent Deloitte study “Accelerating smart manufacturing – The value of an ecosystem approach“ (2020), energy management (36%) and quality control (34%) emerged as particularly relevant use cases, which are already being implemented by many of the companies surveyed worldwide.
In the context of the Corona pandemic this year, many companies had to prove how quickly new, digital approaches can be implemented.
In order for existing processes to be successfully digitalized, they must first be visualized, documented and analyzed (Process Mining) in order to highlight risks as well as potential for improvement and automation. The optimizations identified during the analysis can be implemented in the business processes in the form of digital workflows. In addition, KPIs should be defined and linked to the workflows so that a targeted control is possible.
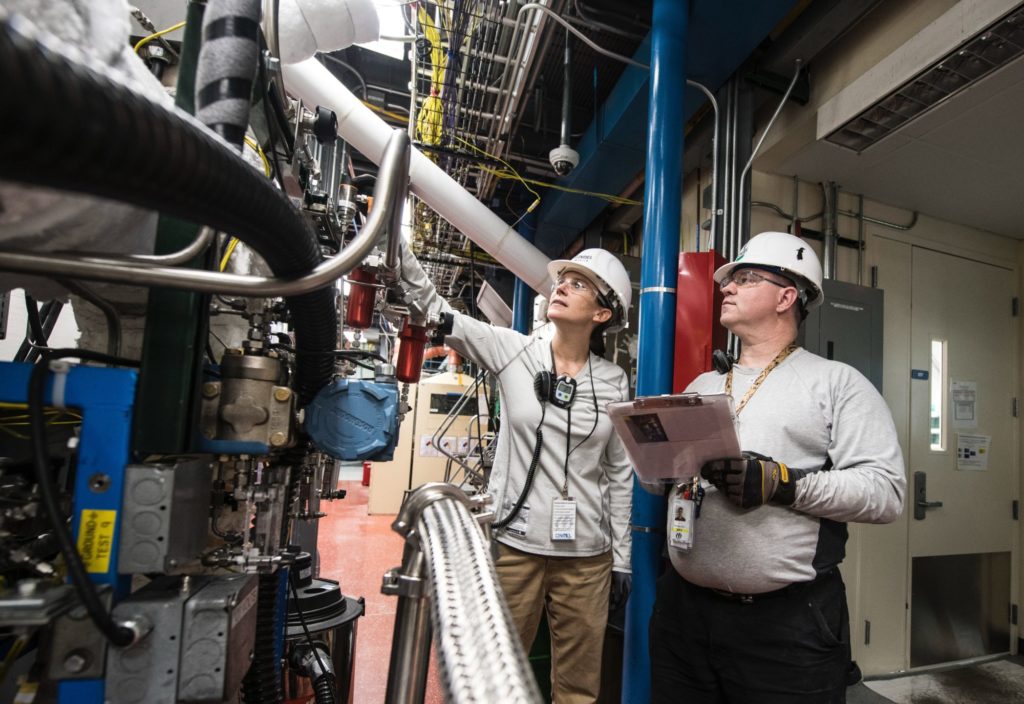
In their “Accelerating smart manufacturing – The value of an ecosystem approach” study, Deloitte identified characteristics that characterize companies with a mature ecosystem approach, including a comprehensive network (“connected everything“) with real-time communication, holistic decision making through cross-divisional information exchange, and an “Always on” agility, which means increased flexibility in adapting to changing market conditions and identifying new opportunities.
Ecosystems are not only relevant for production, but also for supply chains, sales/customers and employees.
While companies invest in networking their machines, a large part of the management, administration and support processes are still handled via Microsoft Excel and Outlook (see also Why Excel is not a management tool). As a result, countless systems, processes and versions coexist, which are handled in parallel instead of being consolidated/networked in one (eco-)system.
Process digitalization with MSO
MSO stands for digitalization, consolidation, transparency and compliance.
With the MSO management software as the “Swiss Army Knife” MSOne4All, companies can create any number of templates for data acquisition, workflow creation and evaluation and thus operationalize and digitalize all their management, administration and support processes – agile, lean and flexible.
- All in One: Consolidation of different applications
- Remote access from anywhere
- Maximum transparency
- Audit and revision security
- Reduction of interfaces, data transfer and evaluation times
- Data availability and traceability (who, what, when): quick overview - quick decisions, preview instead of review, control instead of rework
- Data security and validity
- Targeted reporting
- Quick adaptability (challenges of the VUCA world)